The crushers or the rock crusher are nothing but simply a machine that includes the capability of reducing the size of either the rocks or the stones that one is feeding to the machine. The rocks are reduced using the production, where the recycling is done of the construction material and along with that, the operations of the mining. There are many companies available in the market that provide you with the crusher that is designed and engineered in such a way that can easily crush the river gravel using the crusher wear parts foundry that crushes them into the fine particles. Depending on the requirement of the size and the operations for the crushing of the rocks and stones, different types of the crushers are available in the market.
Different types of the crushers available in the market
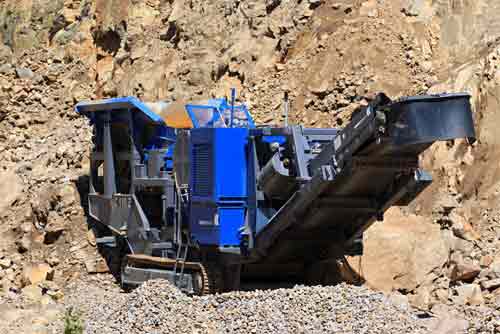
There are a total of four types of the crushers available in the market that you can use for squeezing any abrasive material into any size of the grain and it is purely obtained from the combination of the crusher wear parts foundry you are using. Furthermore, you are required to have a good knowledge of it before operating any crushing operations. The crushers that crushes the rocks are basically of two main groups as such the compression crushers that are capable of pressing the material till it gets break into the small pieces and the other one is the crushers that are design with the impact and they work on the rules and regulations of simply crushing the material without breaking it. The crusher wears parts such as the jaw crusher, gyratory crusher and along with that the cone crusher belongs to the group of the compression crusher and the impact crusher runs on the impact principle.
Talking about the first type, it is the Jaw crusher which is found to be used as the primary crusher and the main function one can observe from it is that it can reduce the material that one is feeding to the machine into smaller size. This small size of the material can be taken to the next stage of the crushing with the help of the conveyors. The second one is the gyratory crusher which is rarely used in the crushing stage of primary and more less than in the crushing stage of secondary. This type of crusher includes the shaft which is oscillating in nature and the material that is been placed inside the crusher can easily be reduced to the place called as the crushing cavity which has its position between the fixed element which is the bowl liner and the internal moving element which is basically the mantle that is being placed on the shaft assembled in an oscillating nature.
The third type of the crusher is the cone crusher which is look alike of the gyratory crusher when considering the technology, but they are used more in the crushing stage of secondary and along with that the other crushing stages as well as such the tertiary and the quaternary. Sometimes, the size of the grain is small that is being processed in the machine and for that there is no requirement of the crushing stage of the primary. If this case ever occurs, then you can run the machine of the first stage of the crushing, and it will give you the result which is well – organized in nature. The last one in the list is the Impact crushing where there is no breaking of the material involved and any stage can be used.